Canada’s Oil Sands Innovation Alliance (COSIA)
As the innovation arm of Pathways Alliance, we advance new technologies and processes that can reduce the environmental impacts of oil sands operations.
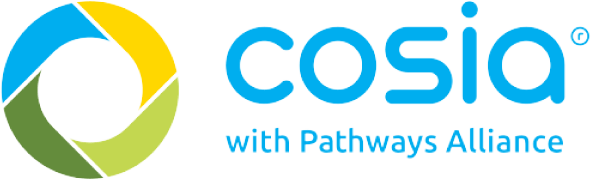
How we work
It’s all about collaboration. We work with academics, researchers, inventors and anyone else who has an idea that can produce incremental or big improvements.
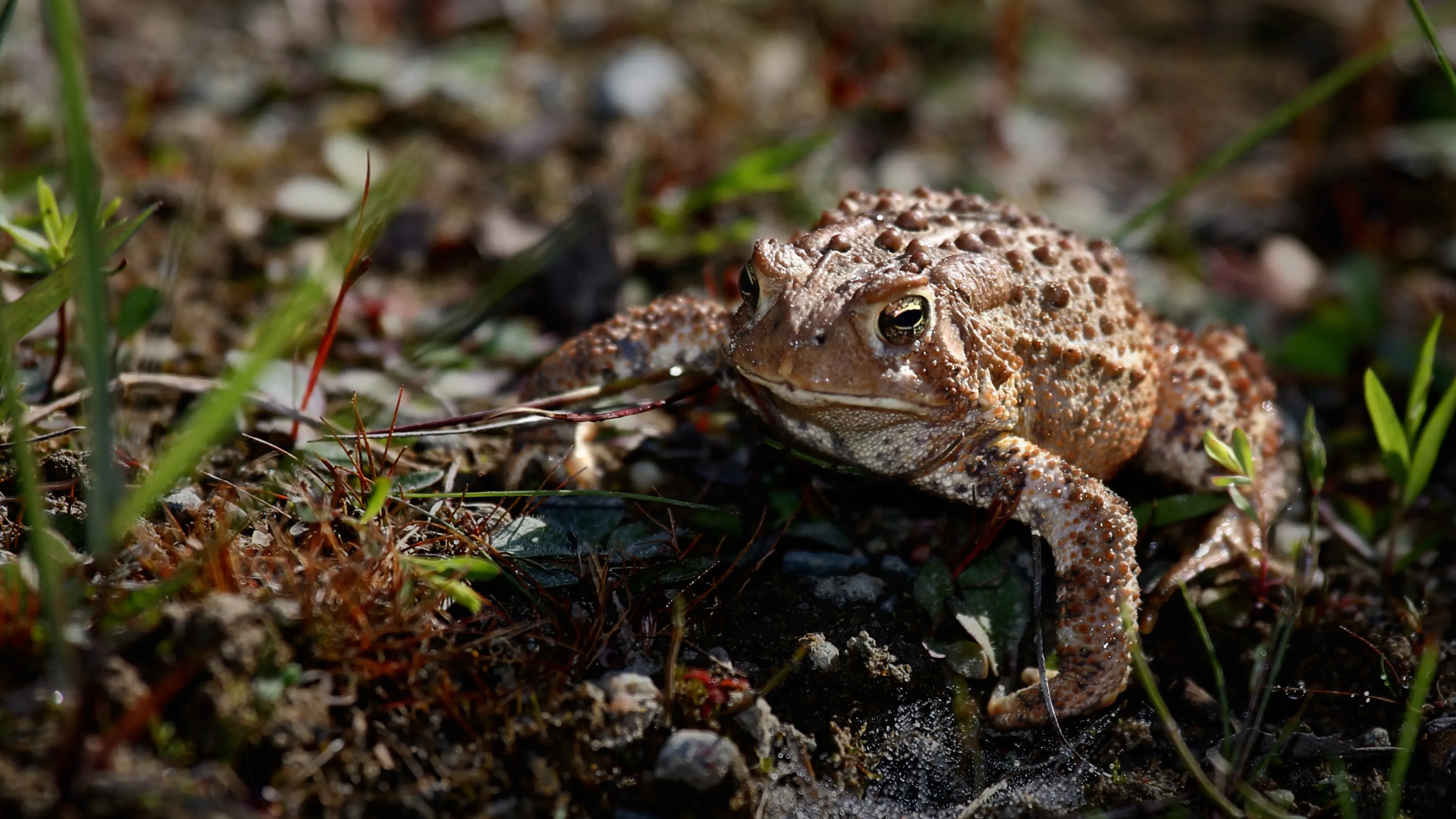
We gave radios to 34 toads
One of the innovative ways that Canadian Natural is using research and technology to manage the impacts of its operations is by monitoring and relocating Canadian Toads at Horizon Oil Sands Site in northeastern Alberta.
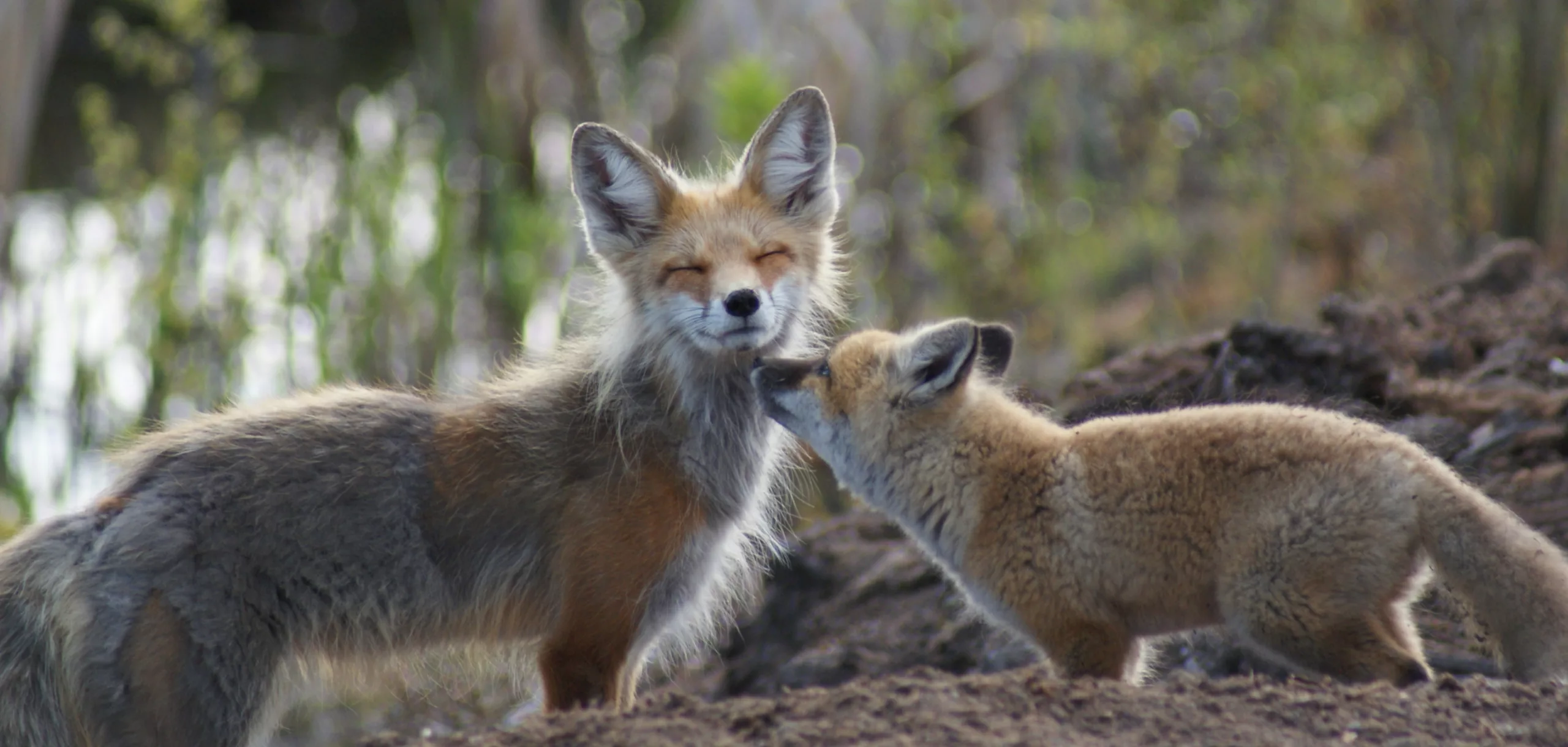
Environmental priority areas
We work to improve measurement, accountability and environmental performance in four priority areas.
Greenhouse gas (GHG) emissions
We’re advancing technologies that continue to reduce GHG emissions and investigating ways to reduce energy use at in situ and mining operations.
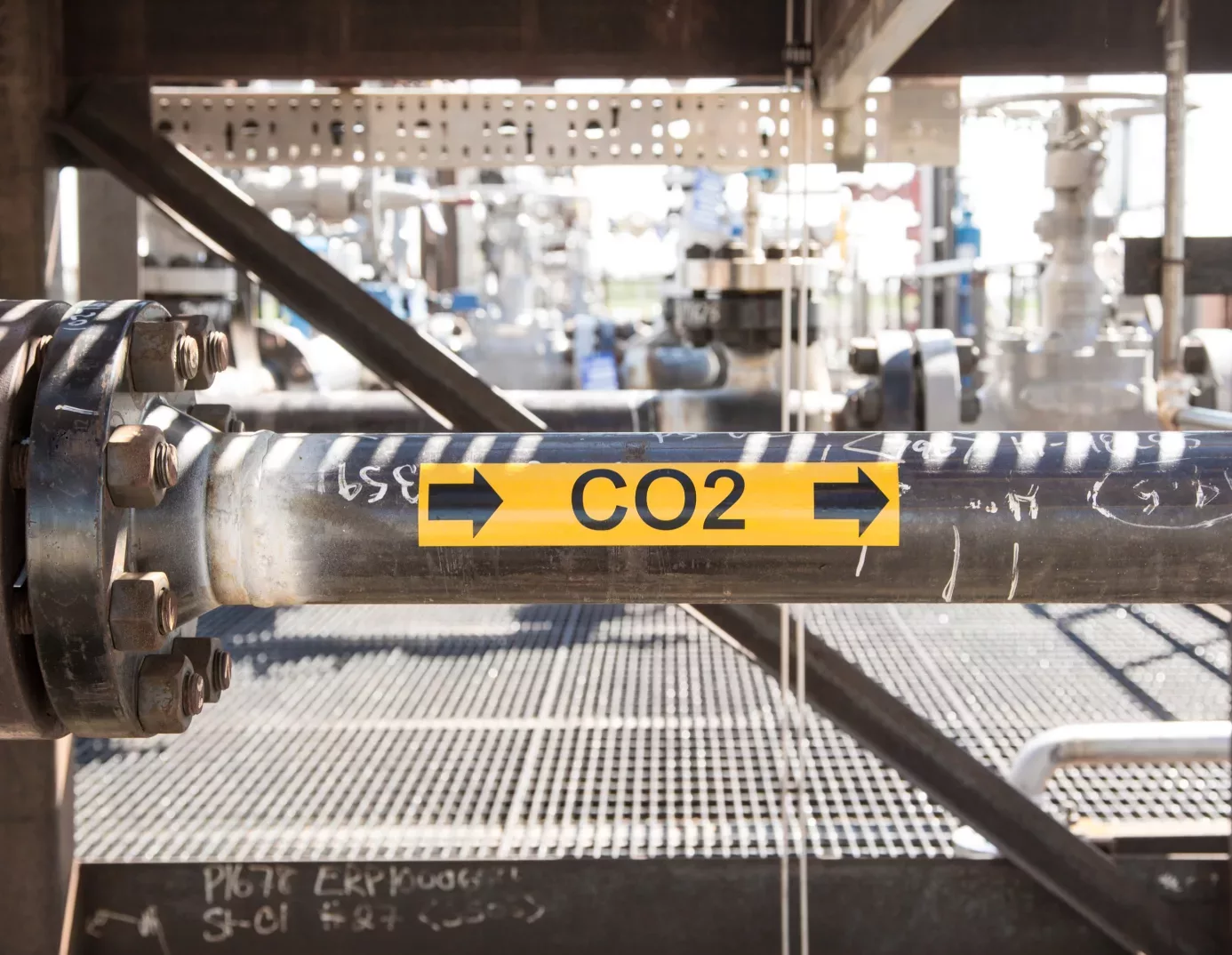
Land
Effective land management and maintaining thriving ecosystems in the oil sands are important parts of responsible development. We’re working to optimize land use, enhance reclamation and preserve biodiversity. We also drive science to improve environmental performance and reclamation outcomes.
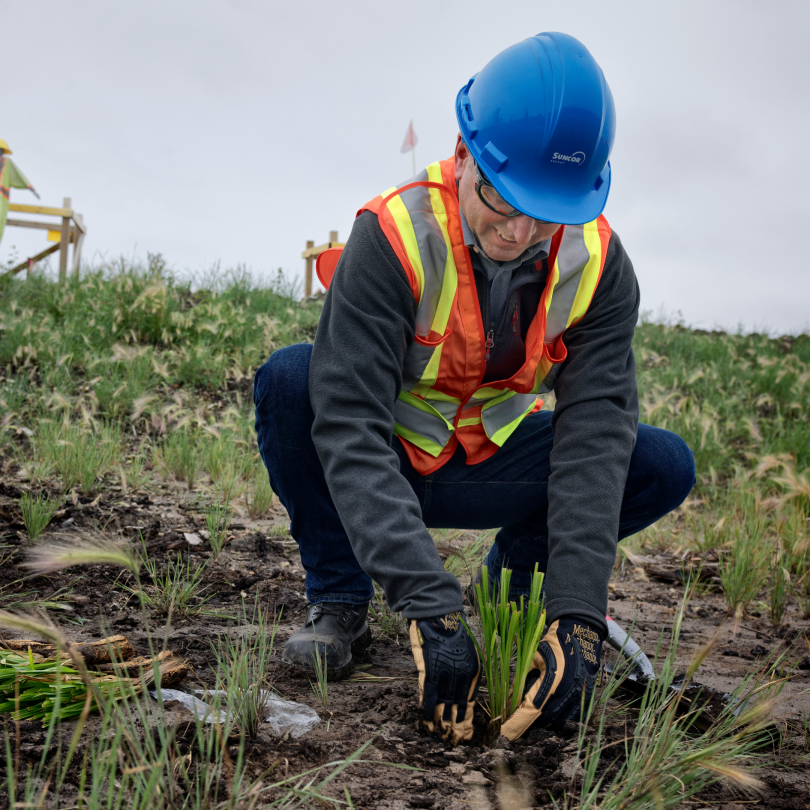
Tailings
Our focus is on enhancing oil sands tailings management through the development of new and improved sustainable technologies. That means developing approaches to reduce tailings volumes, mitigate the environmental impact of tailings production and accelerate tailings reclamation.
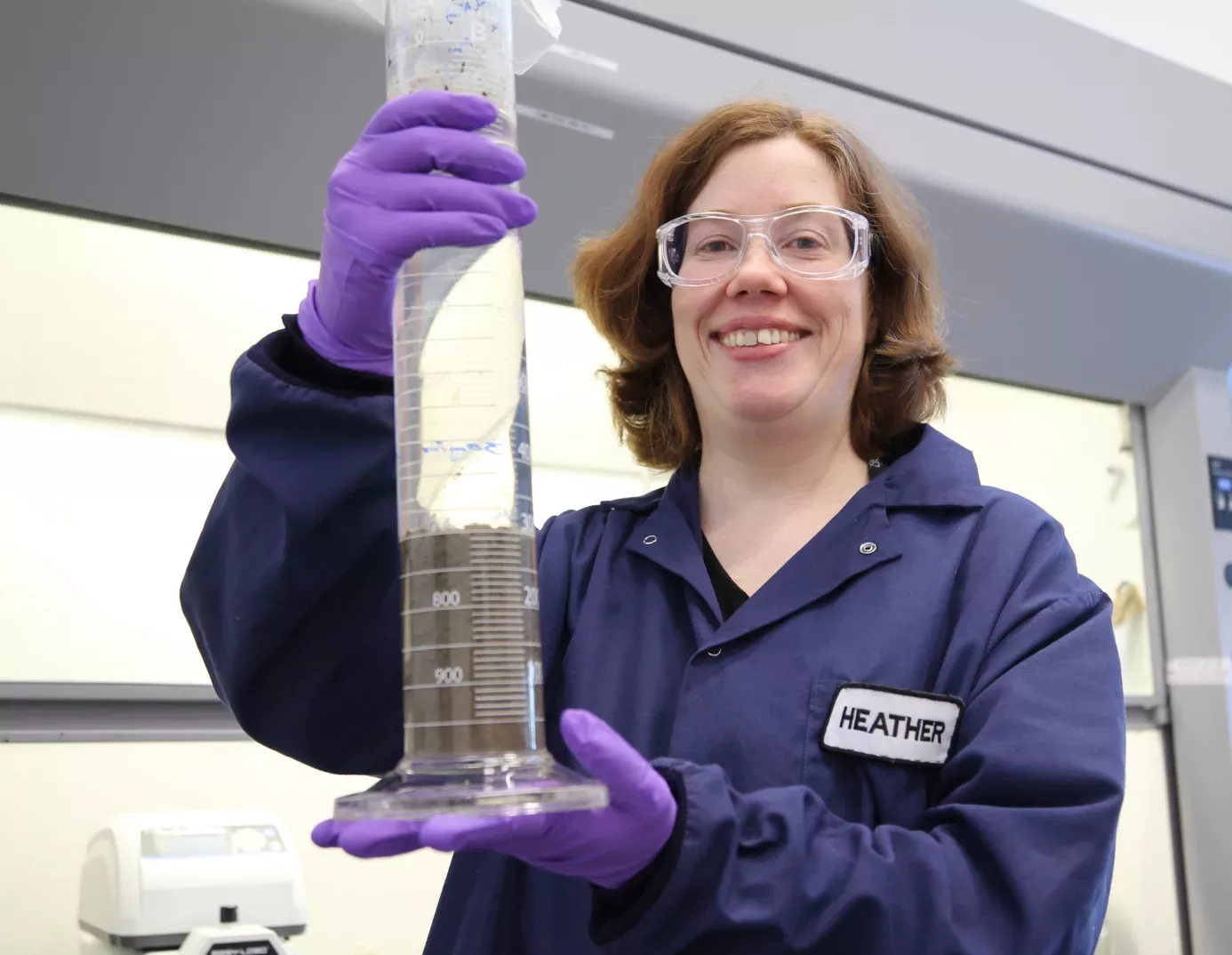
Water
We’re working to improve the use of all water resources to protect the Athabasca River watershed. The goal is sustainable water management, and we’ve already made great progress. The industry has reduced the amount of water used per unit of production and conserves existing water resources as much as possible.
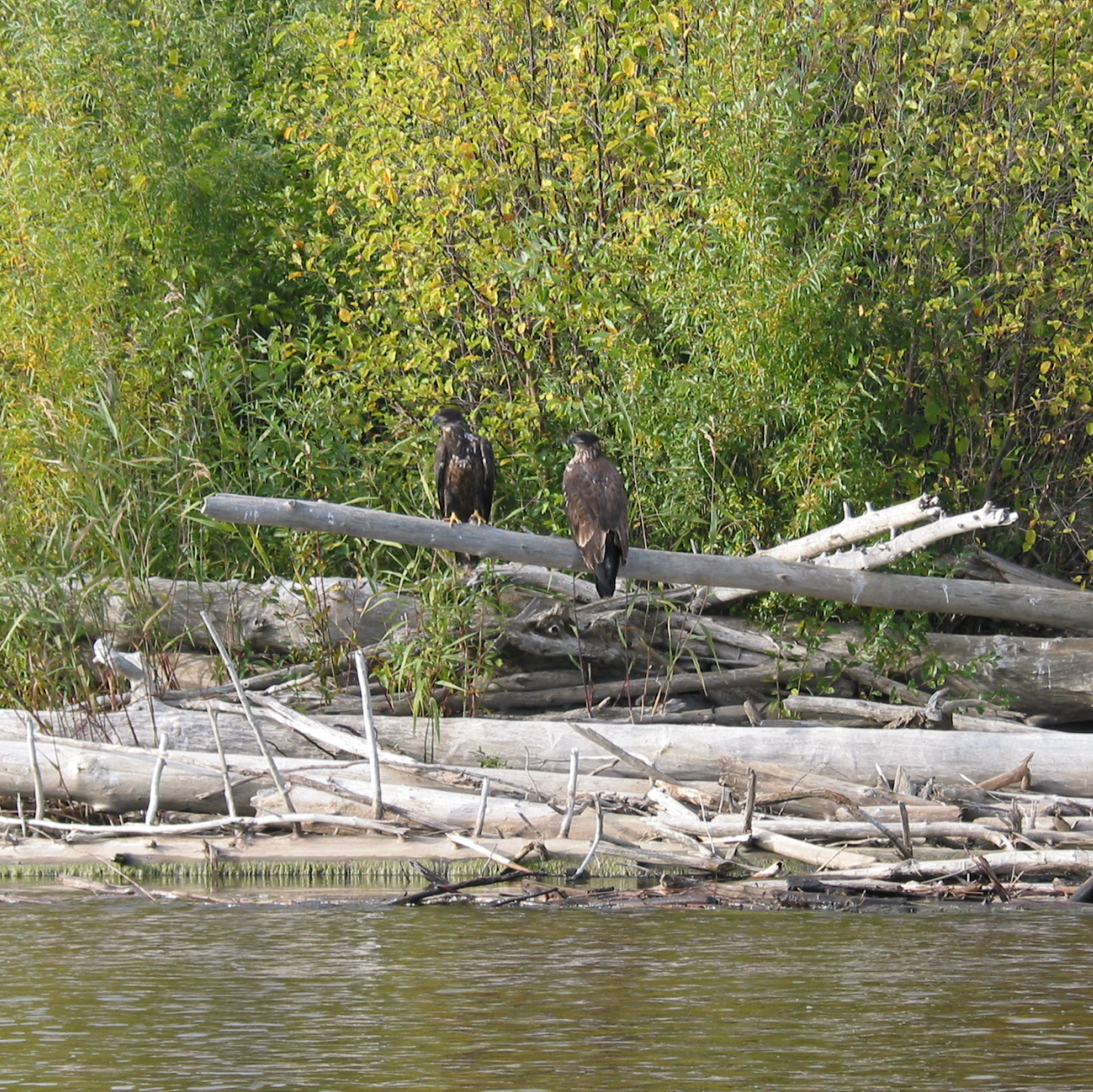
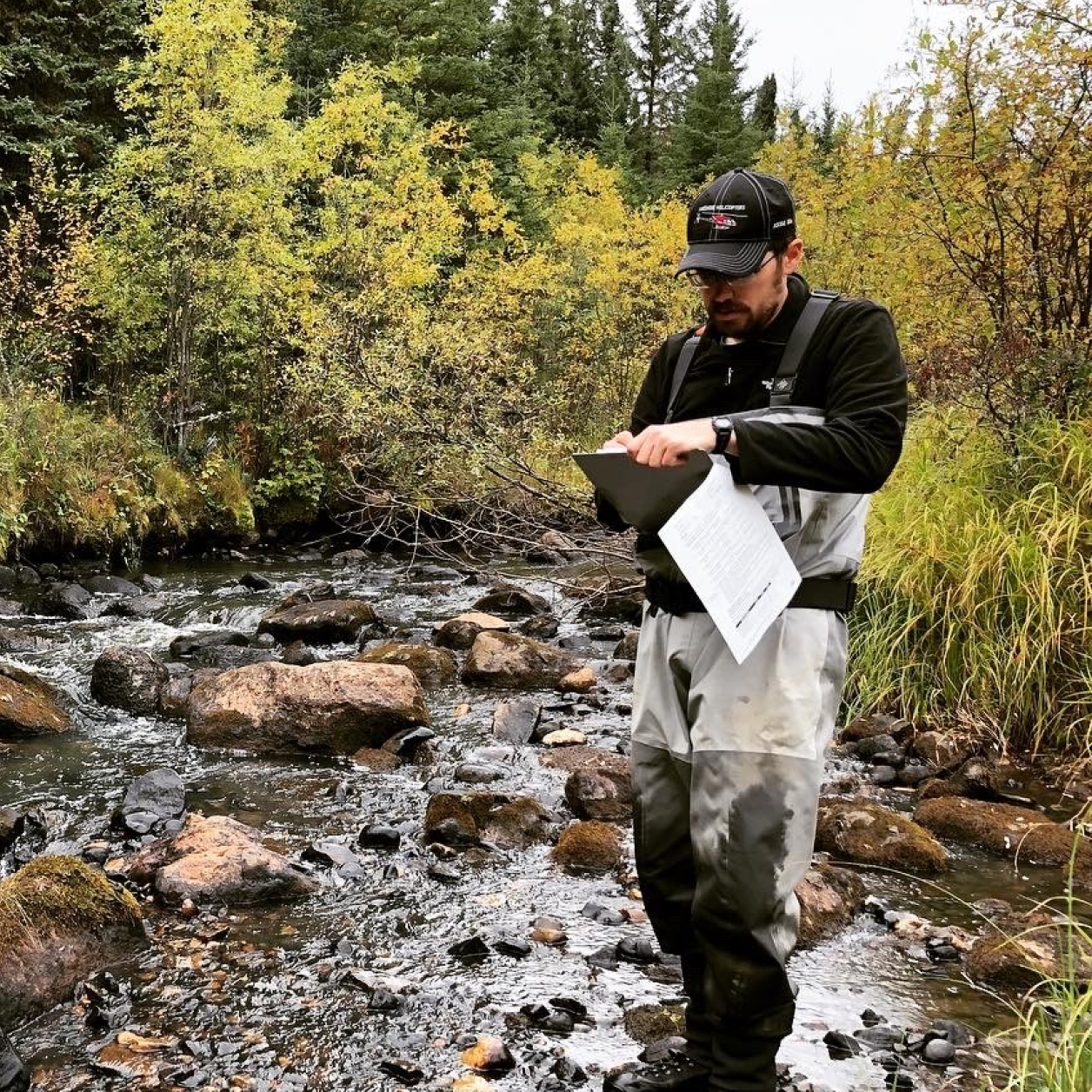
Monitoring
The Oil Sands Monitoring Program (OSM) is one of the largest regional environmental monitoring programs in North America. It monitors and reports on the impact of oil sands development on air, water and land. Our Monitoring Priority Area represents industry in OSM and collaborates with governments, the Alberta Energy Regulator, local communities and Indigenous groups.
Sign up for the COSIA Newsletter
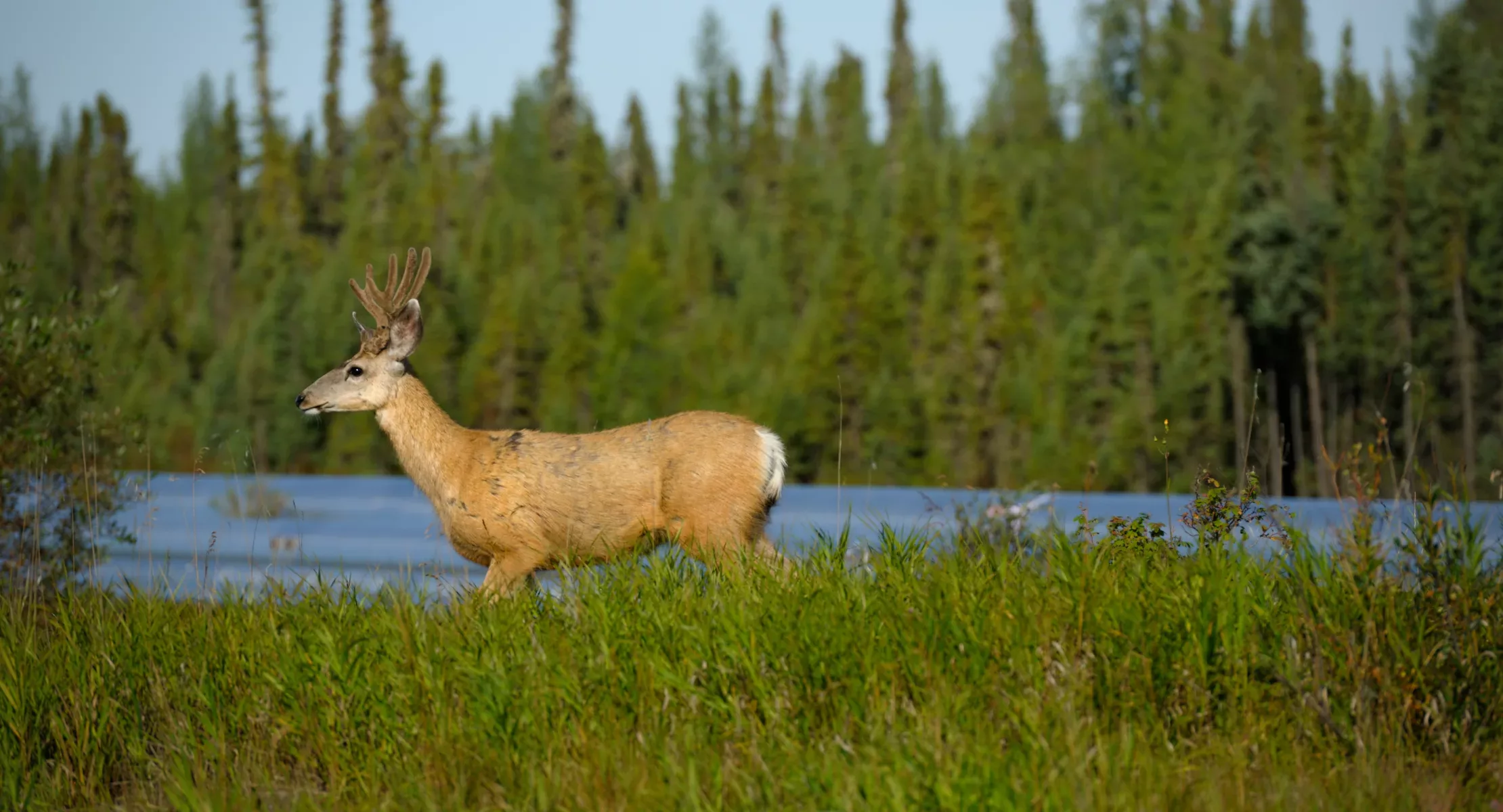
Environmental, Social and Governance (ESG)
Find the latest ESG reports and updates from Pathways Alliance and our member companies.